How Much Does It Cost to Build a Cruise Ship?
- September 14, 2024
- Posted by: admin
- Category: Blog
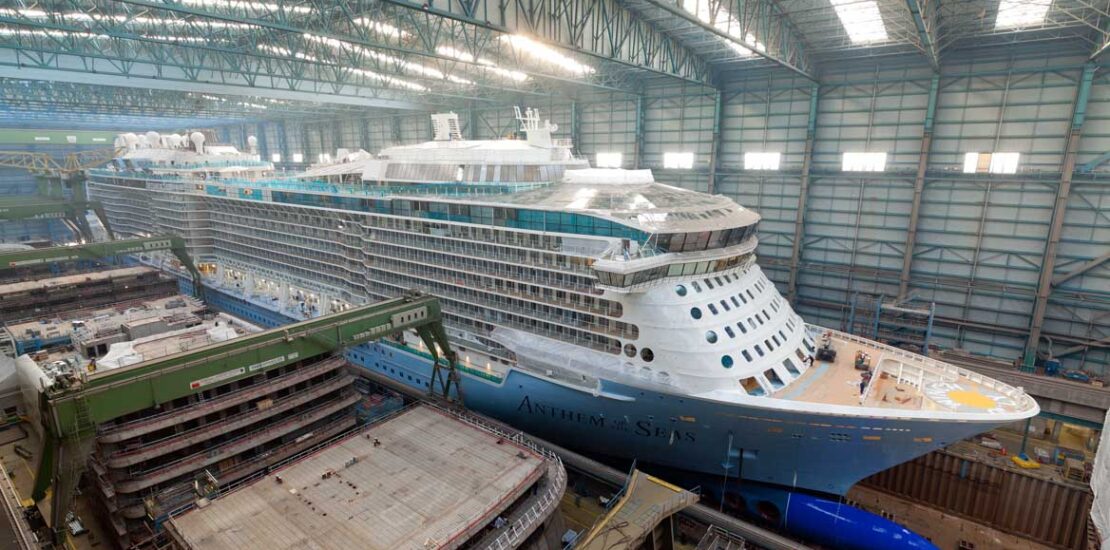
Building a cruise ship involves complex factors such as design, materials, labor, and technology. Each element contributes to the overall cost, which can vary widely. Here, we’ll discuss these components to grasp the intricacies behind the final price tag.
Cruise ship construction costs have evolved significantly over time. In the early 1990s, new ships cost about $300 million, now equivalent to higher figures due to inflation. The 2000s saw larger vessels with average costs surpassing $500 million.
Presently, the latest ships can top $1 billion, but expenses fluctuate, especially for ships accommodating over 3,000 passengers. These typically exceed $750 million in building expenses.
Building a cruise ship is a complex endeavor influenced by a multitude of factors that significantly impact the final cost. From the ship’s size to the intricacies of its design, various elements contribute to the expenses involved in creating these ocean-faring marvels.
The size of a cruise ship is perhaps the most obvious determinant of its construction cost. Larger vessels require more materials and labor, resulting in higher expenses. Moreover, a ship’s passenger capacity also plays a crucial role.
Ships designed to accommodate over 3,000 passengers tend to have costs exceeding $750 million due to the heightened demands on infrastructure, amenities, and safety features.
Innovative and intricate ship designs can significantly drive up construction costs. Cruise lines are constantly pushing boundaries to offer passengers unique experiences, such as onboard attractions, entertainment venues, and specialty restaurants.
The integration of these features demands advanced engineering and design expertise, contributing to elevated expenses.
The choice of materials used in construction can greatly impact costs. High-quality materials that ensure safety, longevity, and energy efficiency often come at a premium. Additionally, the use of environmentally sustainable materials and technologies, while commendable, can also increase overall expenses.
As technology advances, cruise ships incorporate cutting-edge systems for navigation, propulsion, communication, and passenger comfort. Implementing these technologies requires specialized expertise and investment, leading to higher construction costs.
Cruise ships are subject to stringent maritime regulations and safety standards. Compliance with these regulations necessitates additional engineering, construction, and testing processes, which can contribute to elevated costs.
The skilled labor required for building a cruise ship is extensive and diverse, including naval architects, engineers, welders, electricians, and more. Acquiring and retaining these skilled professionals contributes to the overall cost of construction.
The luxurious amenities and interior design elements aboard modern cruise ships are key selling points. Lavish cabins, entertainment spaces, spas, and dining options enhance the passenger experience, but they also drive up costs due to the meticulous attention to detail and premium materials involved.
Global economic conditions can impact the cost of materials, labor, and logistics, thereby affecting cruise ship construction costs. Fluctuations in currency exchange rates, inflation, and supply chain disruptions can lead to unpredictable expenses.
Cruise ship companies often embark on extensive renovation projects to keep their vessels appealing, competitive, and in line with evolving passenger expectations. Renovating cruise ships is a strategic decision that addresses various factors influencing the maritime industry and customer preferences.
In a rapidly evolving travel industry, cruise ship companies recognize the importance of staying competitive. Renovations allow them to modernize their fleets and remain relevant in a market where travelers seek novel experiences and amenities.
Upgrading ships ensures that they can offer state-of-the-art facilities and attract passengers who demand more than just transportation.
The core of cruise ship renovations is enhancing the passenger experience. By introducing new entertainment options, dining venues, wellness facilities, and interactive technologies, cruise lines can create a more captivating and enjoyable journey for their guests.
Renovations also enable cruise companies to respond to changing passenger demographics and preferences, ensuring that their ships continue to cater to a wide range of travelers.
Renovating existing cruise ships can be a cost-effective alternative to commissioning entirely new vessels. Building a new cruise ship from scratch is a substantial investment in terms of time, resources, and capital.
Renovations allow companies to update and modernize ships while leveraging their existing infrastructure, which can result in considerable savings compared to building entirely new ships.
As the maritime industry faces increased scrutiny regarding its environmental impact, cruise ship companies turn to renovations to implement more sustainable and energy-efficient technologies.
Upgrades that reduce fuel consumption, emissions, and waste can align with growing environmental awareness and regulations, demonstrating the industry’s commitment to responsible practices.
Renovating cruise ships helps maintain brand loyalty and encourages repeat business. Passengers who have had positive experiences on a particular cruise line are more likely to return if they see ongoing efforts to improve and innovate.
Renovations also generate excitement and anticipation among loyal customers, driving higher bookings and occupancy rates.
Renovating cruise ships allows companies to adapt to fluctuating economic conditions. During challenging times, when investing in new ships might not be feasible, renovations offer a way to update and revitalize existing assets without committing to the high costs of new builds.
Renovations offer an opportunity to ensure that cruise ships comply with evolving maritime regulations and safety standards. By incorporating necessary upgrades, cruise companies can continue to operate following industry guidelines and international regulations, enhancing passenger safety and satisfaction.
Royal Caribbean International, founded in Norway and headquartered in Miami, Florida, USA, leads the cruise industry in revenue. With 26 ships in operation, its Oasis Class stands out, boasting the world’s 4 largest cruise ships: Oasis of the Seas, Allure of the Seas, Harmony of the Seas, and Symphony of the Seas.
Royal Caribbean takes the crown for both size and cost, as these elite ships are priced at over $1 billion each. Now, let’s delve into the remarkable features of the Oasis Class vessels.
- Cost: $1.4 billion
- Launched: 2008
- Capacity: 6,780 passengers, 2,700 rooms
- Size: 1,187 feet long, 208 feet wide
- Weight: Over 225,282 tons
- Launched: 2010
- Cost: $1.4 billion
- Capacity: 5,492 passengers, 2,384 crew
- Size: Not specified
- Launched: 2016
- Cost: $1.35 billion
- Capacity: 5,479 passengers, 2,100 crew
- Size: 1,188 feet long, 226,963 tons, 2,278 rooms
- Cost: $1.5 billion
- Launched: 2016
- Capacity: Nearly 9,000 (passengers and crew)
- Cabins: 2,759
- Size: 1,188 feet long, over 215 feet wide, over 228,081 tons
While North America leads in cruise industry popularity, European shipyards, such as Meyer Turku [1] in Finland and Chantiers de l’Atlantique in France, build the majority of cruise ships. Cost efficiency drives this trend.
With billion-dollar price tags, ships are constructed overseas due to lower labor and material costs in Europe, aided by industry subsidies.
Foreign flagging, common for cruise ships, avoids higher U.S. construction costs as stringent requirements mandate most materials to be domestically sourced.
Intricately influenced by design, technology, materials, and labor, the cost of building a cruise ship varies widely. Factors like size, innovation, and compliance with regulations drive expenses.
An understanding of these elements unveils the complexities underlying the final investment required for these maritime marvels.